Top 10 Compliance Best Practices for Food, Beverage, & Drugs
Feb 28, 2025
Safety recalls, mislabeling crises, and now rising environmental mandates can overwhelm even well-established companies in the food, beverage, and drug sectors.
A single lapse, whether Salmonella in peanut butter or undisclosed PFAS chemicals in packaging, can erase years of brand loyalty.
But, the pace of regulatory change can feel overwhelming for many.
Some worry that compliance measures will slow growth or stifle innovation.
Yet a well-planned compliance strategy often proves to be a catalyst for better products and stronger customer loyalty.
Below are 10 product compliance management best practices to help you remain agile, confident, and prepared for emerging rules in 2025.
1. Track Regulatory Updates with a Systematic Process
Regulations in food, beverage, and drug manufacturing evolve quickly.
Federal laws like the Food Safety Modernization Act (FSMA) introduce rolling requirements, while amendments to the Toxic Substances Control Act (TSCA) add new chemical reporting obligations.
State-level actions, such as California’s PFAS ban (AB 1817), further complicate the landscape.
Missing even one update can result in product hold-ups, wasted packaging, or forced recalls.
Why It Matters
Consumer Trust: Up-to-date compliance preserves your brand image and minimizes recall risk.
Operational Efficiency: Knowing imminent changes, like the SEC’s climate disclosure mandates, helps you budget for new processes or materials.
Market Access: Major retailers and government contracts often require proof of compliance with evolving environmental and safety standards.
For example, you’ve overlooked the FDA’s proposed new definition of “healthy.”
So you printed 100,000 labels referencing “healthy” ingredients that no longer met updated nutrient thresholds for snacks.
As a result, the entire batch required reprinting, leading to a financial loss and a delay in getting products on shelves.
What To Do?
Create a Regulatory Calendar: Track deadlines from the FDA, EPA, USDA, and relevant state laws.
Subscribe to Alerts: Tools like GovTrack or FDA email lists send instant notifications on proposed rules or final actions.
Designate a Compliance Lead: Appoint an internal champion or external consultant who regularly reviews the Federal Register and industry association updates.
Pro Tip
Although these are all great starting points, manually creating a regulatory calendar, juggling multiple alerts, and designating a compliance lead can be grueling.
Every new rule demands repeated document checks that slow growth and risk human error. Signify automates these steps, using AI to cut review times by up to 90% while maintaining real-time compliance.
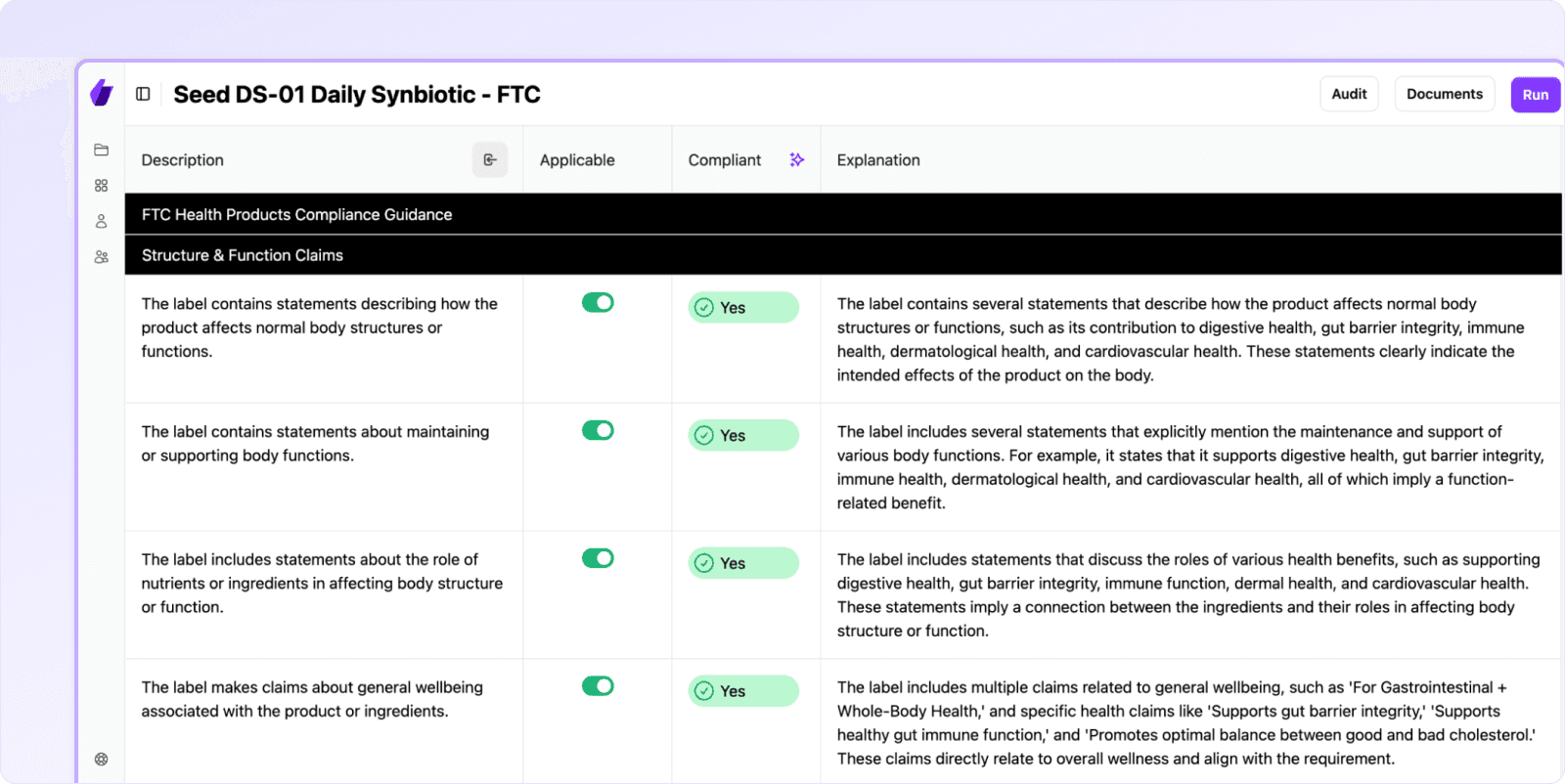
Instead of sinking weeks into manual tasks, you can launch products faster, with higher accuracy, and focus on what truly drives your business forward.
2. Strengthen Supply Chain Transparency and Ingredient Traceability
Supply chain breakdowns frequently cause foodborne illness outbreaks and chemical contamination incidents.
With new demands for PFAS-free packaging and enhanced FSMA traceability requirements, it’s now more critical than ever to document each stage of production.
A single compromised ingredient can lead to extensive recalls if you can’t isolate affected batches quickly.
Why It Matters
Recall Minimization: Clear traceability lets you recall only specific lots rather than entire product lines.
Regulatory Compliance: The FDA’s Food Traceability Final Rule obliges tighter tracking of high-risk foods.
Environmental Accountability: Under TSCA Amendments, you must ensure suppliers aren’t using chemicals now banned or heavily restricted (e.g., PFAS).
For example, your juice brand imported purees from multiple brokers but kept inconsistent lot tracking.
When the FDA flagged elevated lead levels, the company couldn’t pinpoint which shipments were in each blend.
A recall ensued, covering nearly five months of production and costing millions in refunds and retailer losses.
What To Do?
Consolidate Data: Use a unified digital platform to capture each batch’s origin, testing reports, and shipping details.
Conduct Supplier Audits: Verify that every vendor meets both food safety (FSMA) and environmental (TSCA, RCRA) standards.
Implement Real-Time Tracking: Technologies like blockchain or cloud-based traceability systems can automate lot-level oversight.
Pro Tip
Stop sifting through endless PDFs and spreadsheets for compliance references.
Here’s the secret: Automate evidence traceability with Signify.
Our advanced document extraction pinpoints the exact sections containing compliance data, so you spend minutes – rather than hours – proving conformity.
No more guesswork, no more confusion. Just rock-solid audit trails and swift, accurate compliance every single time.
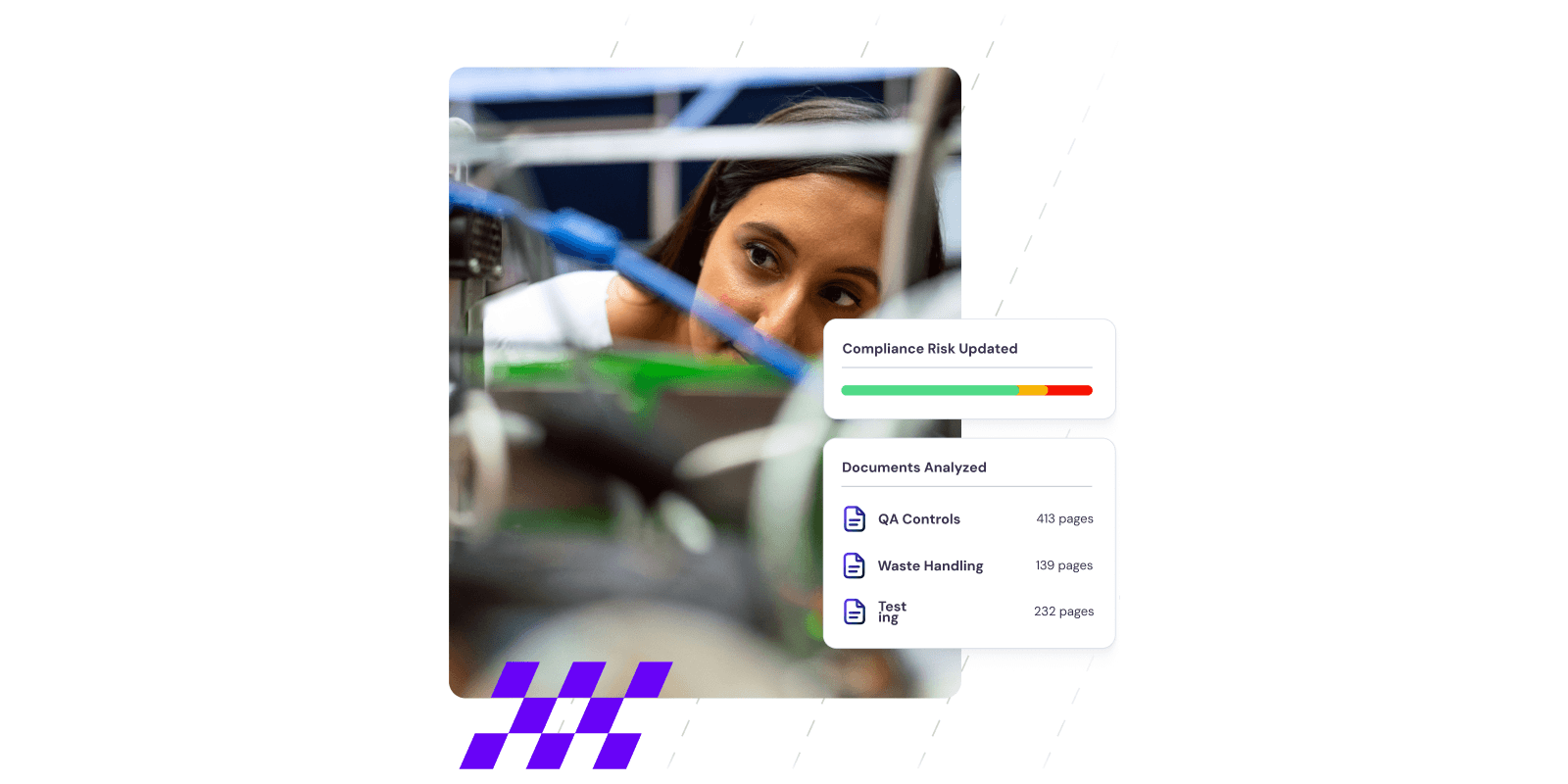
3. Rigorously Control Allergens and Cross-Contamination
Allergen recalls are among the top reasons for market withdrawals in the U.S.
The addition of sesame as the ninth major allergen heightens labeling and production complexities.
A single uncleaned machine or misread formula can prompt a Class I recall and tarnish a brand’s reputation.
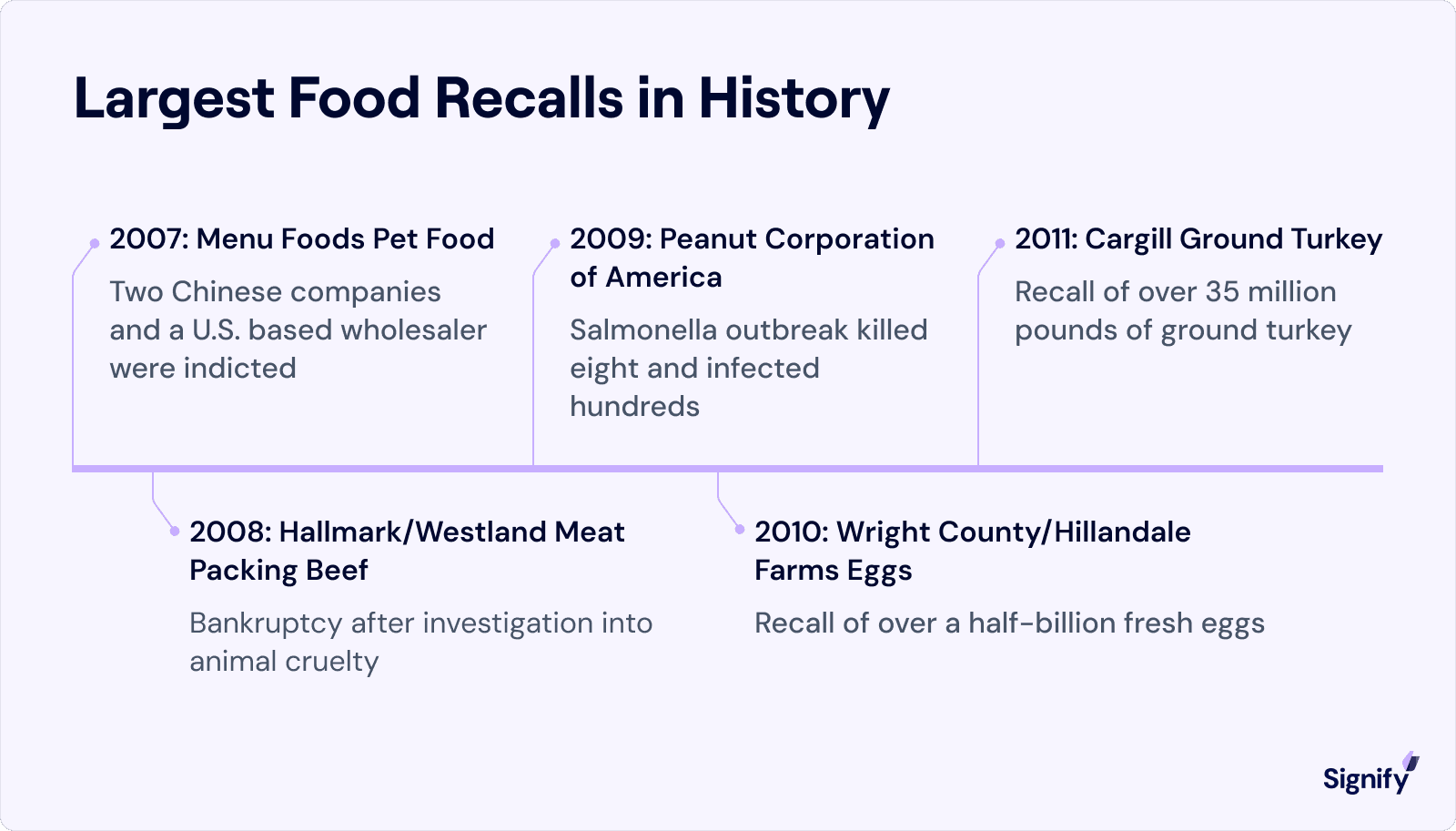
Why It Matters
Consumer Safety: Allergic reactions can be fatal. Proper management ensures consumer well-being.
Regulatory Compliance: The FDA enforces allergen labeling under the Food Allergen Labeling and Consumer Protection Act (FALCPA).
Operational Costs: Avoiding cross-contamination spares you from discarding contaminated batches and paying recall-related penalties.
What To Do?
Dedicated Lines & Scheduling: Produce allergen-free items first or on separate equipment to minimize risk.
Environmental Swabbing: Test surfaces for allergen residues regularly, especially after cleaning.
Frequent Label Updates: Implement a final check step in your SOP whenever formulations or suppliers change.
4. Maintain Strict cGMP Compliance (Food, Beverage, and Drug)
Current Good Manufacturing Practice (cGMP) standards govern facility design, sanitation, and recordkeeping.
These standards vary slightly across food (21 CFR Part 117), dietary supplements (Part 111), and pharmaceuticals (Parts 210–211).
cGMP violations can trigger FDA Form 483 observations or warning letters, which can slow production and damage brand credibility.
Why It Matters
Safety Assurance: cGMP processes reduce microbial, chemical, and physical hazards.
Legal Protection: Evidence of strong cGMP adherence can mitigate penalties if something goes wrong.
Environmental Considerations: Proper chemical handling under cGMP aligns with TSCA rules, preventing toxic leaks or unauthorized discharges.
Suppose you run a dietary supplement firm that expanded production but did not upgrade its air filtration systems.
Cross-contamination between herbal extracts led to inaccurate ingredient levels in finished products. The FDA’s subsequent inspection cited numerous cGMP violations, forcing a costly facility overhaul and a multimonth production halt.
What To Do?
Frequent Internal Audits: Monitor cleaning logs, equipment calibration, and record integrity.
Employee Training: Provide routine cGMP refreshers, ensuring staff understand how to prevent cross-contamination and maintain documentation.
Corrective & Preventive Action (CAPA): Investigate any breach of protocol thoroughly. Revise SOPs and re-train staff as needed to prevent recurrence.
5. Prepare a Robust Recall and Crisis Management Program
Even the best processes can fail. From Salmonella in nut butter to Cronobacter in infant formula, crises can strike when least expected.
A well-designed recall program can contain issues swiftly, safeguard consumers, and maintain customer trust.
Why It Matters
Minimize Harm: A quick, decisive recall limits exposure and protects brand integrity.
Regulatory Expectation: The FDA, USDA, and even the EPA (for chemicals in packaging) expect companies to have recall protocols ready.
Speedy Response: In our hyperconnected world, slow communication can lead to viral negative press.
The 2022 Jif peanut butter Salmonella outbreak demonstrated how swiftly contamination in a single facility can affect multiple downstream products, like snack packs or peanut butter cups. Jif’s parent company deployed a recall toolkit with real-time lot traceability, enabling clear notices on which SKUs were affected.
Despite the size of the recall, well-organized procedures helped reduce long-term reputational damage.
What To Do?
Designate a Recall Team: Include legal, QA, marketing/PR, and logistics roles. Assign responsibilities upfront.
Create Scenario Plans: Run annual recall drills to test traceability, consumer communication, and retailer coordination.
Transparent Messaging: Prepare press releases and social media templates to inform the public quickly.
6. Label with Precision: Nutritional Facts, Claims, and Warnings
Labels are a vital communication channel for consumers. The FDA and FTC scrutinize any health or disease-related claims, especially for dietary supplements and functional foods.
Why It Matters
Consumer Trust: Accurate claims build loyalty; misleading ones spark lawsuits.
Regulatory Enforcement: The FDA’s definition of “healthy” continues to evolve. Violations can lead to warning letters or product seizures.
Chemical Disclosures: Some states require labeling for PFAS or hazardous substances to comply with local bans or advisories.
For instance, there is a flood of refreshing drinks that advertise themselves as “boosting immunity” without substantial clinical evidence. The FTC can penalize the company for false advertising, demanding they either prove the claim or remove it.
What To Do?
Label Review Board: Assemble marketing, legal, and R&D to approve every new label or reformulation.
Clear Allergen Declarations: If a product includes a top-nine allergen (milk, eggs, fish, crustacean shellfish, tree nuts, peanuts, wheat, soybeans, sesame), bold it and list it clearly.
Substantiate Claims: Keep a file of published studies or clinical trials to back up any “reduces cholesterol” or “supports heart health” statements.
Pro Tip
Tired of labeling mishaps delaying your shipments?
Use Signify to scan product labels against FDA and FD&C Act rules instantly, then track changes in country-specific import laws.
The result: fewer errors, faster customs clearances, and confidence that your labels always meet each market’s requirements.
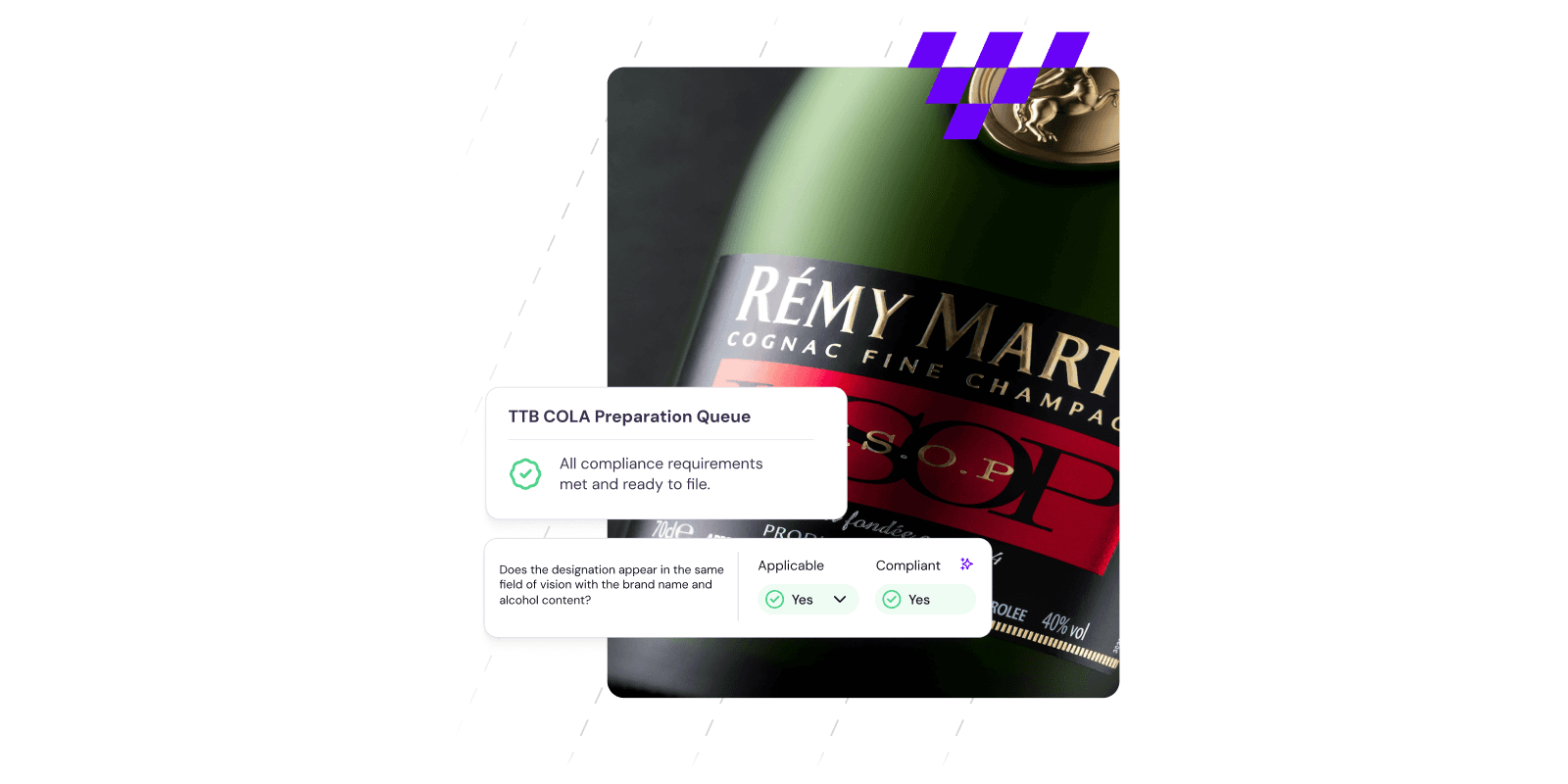
7. Harness Data Analytics and QMS for Early Detection
Modern Quality Management Systems (QMS) and data analytics platforms can automate checks for contamination, temperature excursions, or label inconsistencies.
This approach is especially crucial for preventive controls under FSMA and can also track chemical usage, helping you comply with EPA regulations like the Resource Conservation and Recovery Act (RCRA).
Why It Matters
Real-Time Insights: Automated alerts catch deviations (e.g., a bacterial spike) long before a full batch is jeopardized.
Regulatory Documentation: Digital data logs indicate due diligence during FDA or EPA audits.
Cost Efficiency: Early detection of errors limits product waste and recall size.
What To Do?
Integrate QMS: Consolidate lab results, batch records, and environmental monitoring in a single platform.
Set Threshold Alarms: Define acceptable temperature, pH, or microbial count ranges; system alerts trigger immediate investigation.
Periodic Trend Analysis: Beyond real-time alerts, review monthly or quarterly data to spot subtle but persistent shifts.
8. Invest in Ongoing Workforce Training and a Culture of Compliance
Regulatory frameworks evolve, and so does your team.
Ignorance of rules is never a valid legal defense. Regular, interactive training ensures employees remain your first line of defense – not a liability.
Why It Matters
Human Factor: Most cross-contamination incidents or labeling mistakes stem from employee oversights.
FDA & EPA Expectations: Both agencies often cite inadequate training in warning letters and fines.
Empowered Reporting: A trained workforce is more likely to flag suspicious changes, like mislabeled chemicals or allergen infiltration, before they escalate.
What To Do?
Interactive Sessions: Use videos, quizzes, or VR simulations for practical training rather than dull lectures.
Open-Door Policy: Encourage employees to report near-misses or concerns. Reward those who proactively solve problems.
Track Attendance & Scores: Keep records of who completed which modules – evidence of ongoing compliance efforts.
9. Align with Retailer and Consumer Demands
Big retailers like Walmart, Costco, or Whole Foods often enforce higher standards than federal baselines.
Meanwhile, consumers expect claims about “organic,” “natural,” or “sustainably sourced” to be genuine and verifiable. Meeting these demands can significantly boost brand reputation and sales.
Why It Matters
Shelf Access: Non-compliance with retailer standards can result in lost listings.
Brand Loyalty: Shoppers reward transparency and ethical sourcing.
Environmental Pressure: PFAS bans, GHG emission targets, and net-zero goals are top-of-mind for large retailers, and, by extension, their suppliers.
Let’s say you are a meat producer who wants to sell at Whole Foods, which requires Global Animal Partnership (GAP) certification.
Achieving it meant overhauling feeding practices, antibiotic protocols, and recordkeeping.
The improvements paid off with higher product margins, brand loyalty, and expanded distribution in premium grocery chains.
What To Do?
Map Retail Standards: List each major retailer’s requirements, some might enforce PFAS-free packaging or advanced traceability.
Third-Party Certifications: Explore recognized seals (e.g., Non-GMO Project, Rainforest Alliance) that align with your product category.
Continuous Consumer Feedback: Monitor social media and customer service logs to gauge sentiment on your environmental and safety claims.
10. Seek Expert Guidance and Foster Continuous Improvement
Compliance in food, beverage, and drug manufacturing intersects with toxicology, environmental science, and regulatory law.
External specialists, whether consultants or accredited labs, can fill knowledge gaps.
Why It Matters
Technical Complexity: Nitrosamine impurities in drugs, PFAS contamination in packaging, and other specialized issues require expert knowledge.
Regulatory Volatility: An executive order can freeze certain environmental rules while others, like TSCA fees, surge ahead. Skilled consultants help parse these changes.
Long-Term Savings: Proactive improvements often cost less than damage control or product recalls.
What To Do?
Third-Party Audits: Schedule unbiased facility reviews at least annually.
Academic Collaborations: University labs can test new green packaging solutions or novel sanitization methods.
CAPA Log: Track every corrective/preventive action. Evaluate success rates and re-train staff on revised protocols.
Partner with Signify: Our AI-driven solution streamlines conformity assessments, documentation reviews, and labeling checks, easing your compliance workload and boosting accuracy.
Conclusion
Regulatory compliance for food, beverage, and drug products isn’t just about product safety anymore.
Recalls have proven how quickly trust can crumble, and 2025 environmental rules, like PFAS bans and climate disclosures, make this topic even more complex.
Embracing strategic best practices now protects consumer health, safeguards your brand, and positions you for a more sustainable future.
How Can Signify Help?
Whether you’re a GRC Manager, Compliance Manager, or Quality Assurance Lead, Signify automates the toughest parts of compliance so you can focus on delivering safe, high-quality products.
Our AI-powered platform transforms bulky regulations into actionable workflows – keeping you audit-ready, reducing manual effort, and helping you adapt to rapid changes with ease.
Key Features
1. Regulatory Compliance Intelligence
Automatically evaluates your products against relevant frameworks (e.g., Title 21 CFR). Maintains audit readiness and reduces compliance risks without manual data crunching.
2. Radar Monitoring
Continuously tracks new regulatory updates, detects risks early, and alerts you before non-conformities arise – no more tedious scanning of rule changes.
3. Checklist Generator
Converts complex laws and standards into straightforward task lists. Simplifies new regulations into manageable steps that anyone on your team can follow.
4. Conformity Auditor
Monitors internal documents (SOPs, labels, artwork) to ensure they meet industry standards, highlighting any gaps and suggesting corrective actions.
5. Automated Compliance Testing
AI-driven evaluations of your compliance documentation, ensuring proactive identification of risks and reducing the chance of last-minute surprises.
6. Remediation Guidance
Identifies exactly where you’re falling short and outlines clear, step-by-step fixes—keeping your operation aligned with evolving rules.
Ready to Simplify Your Compliance Journey?
Book a demo today to see how Signify automates regulatory tasks, mitigates risks, and helps you maintain the highest standards of food safety and compliance.